Aerial thermography inspection is the most efficient way for solar PV operations and maintenance (O&M) teams to identify and repair malfunctioning solar modules. Aerial inspection is nearly 10 times faster than traditional inspection methods and provides high-quality actionable insight that can be used to maximize site performance. While it is well established that aerial thermography can save asset managers money, have you ever wondered how much? By drastically reducing the amount of labor hours necessary for inspection and optimizing site yield through proactive maintenance, many O&M providers will see a swift return on their investment. Aerospec estimates that proper implementation of aerial inspection can save solar operators over $1,900 per MW.
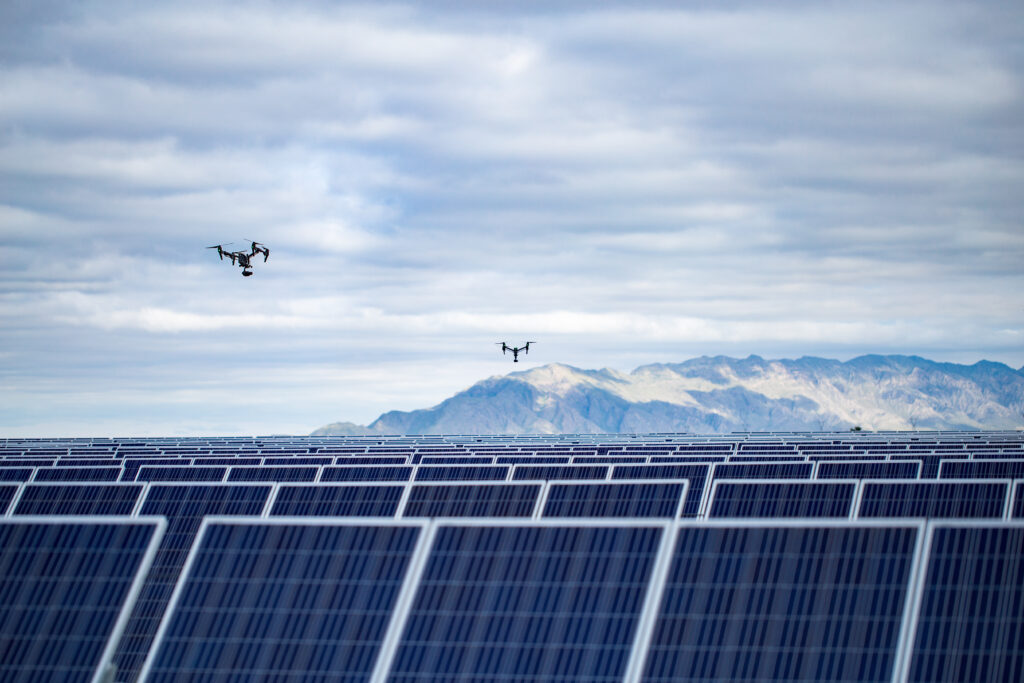
To estimate savings per megawatt, we scanned a variety of industry reports and examined data provided by our clients through in-depth interviews. We found that most of the savings come from the difference in hourly rates, hardware, and software costs between traditional inspection and aerial thermography inspection. While there are hardware and software costs that are mostly unique to aerial thermography, manual inspections command a much higher hourly rate and are more time consuming. Additional savings were found to have accrued as a result of the completeness of the inspections and their faster turnaround times — aerial thermography helps O&M providers save by finding more faults and fixing them more quickly.
Traditional field inspections are time-consuming, incomplete, and expensive. The industry standard practice is to inspect a small 10-25% sample size of modules to save time. Assuming a 20% sample size is being used, Aerospec Technologies estimates that it takes a technician roughly 25 hours to inspect 1MW on foot. At an average wage of $35/hour, it would cost approximately $8,750 to inspect a fairly small 5MW farm. Note that this is the cost to inspect only a small sample of a site’s modules, and there may still be undetected problems impacting system performance after inspection.
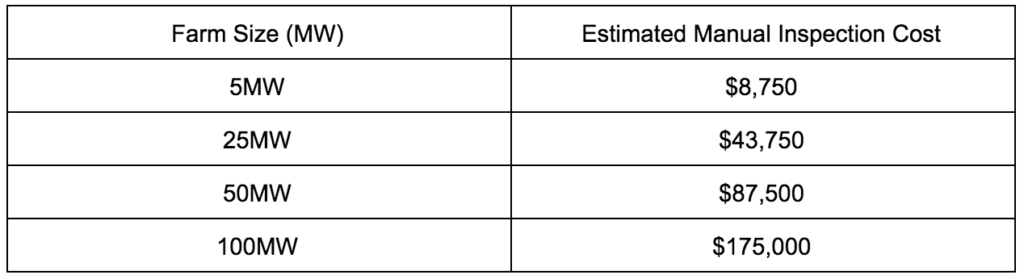
On the other hand, Aerial thermography requires a larger initial investment. O&M managers looking to incorporate aerial inspections into their maintenance procedures must first decide whether to invest in their own hardware and pilots or contract pilot-for-hire services. The industry standard DJI Matrice 210 drone and Zenmuse Flir XT2 thermal camera cost approximately $30,000 together. Aerospec has previously determined that pilot-for-hire services cost an average of $1,862 per day of inspection, not including any additional travel and lodging expenses. Partnering with an aerial inspection solutions provider is also necessary to process and analyze data.
Although the upfront costs of a UAV program are higher than those of traditional field walks, there are several benefits that allow asset managers to get the maximum return on their investment. The greatest advantage of aerial thermography is its speed. A manually piloted drone is able to collect data 10 times faster than a technician on the ground within 97% accuracy. Autonomous inspection tools, such as the Aerospec Pilot app, let unpiloted drones to autonomously conduct pre-planned inspections. Autonomous inspection is nearly 4 times faster than manually piloted drones, and it provides more reliable data and eliminates human error. This increase in speed allows for a total inspection of a site to be completed in a much shorter time frame and ensures that every module has been inspected. Malfunctioning modules that may not have been detected using traditional inspection methods are quickly identified and can be repaired, increasing site yield. One Aerospec client that manages a large portfolio estimates that they save $383,127 annually by repairing defective modules that likely would not have been discovered during on-foot inspections.
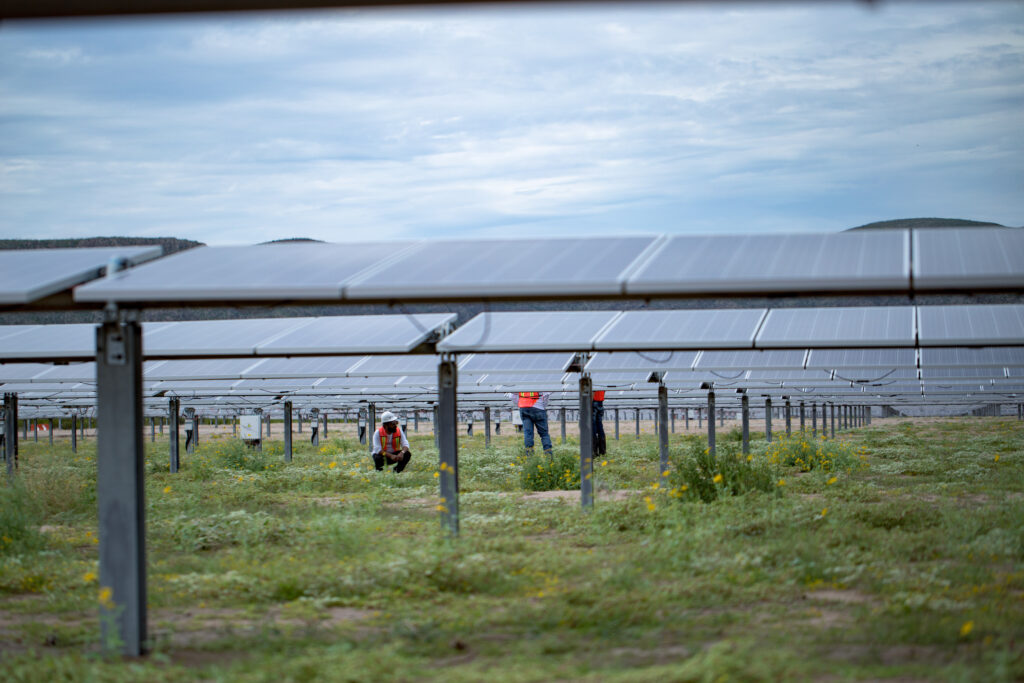
Furthermore, aerial thermography inspection data is capable of rapidly providing actionable information. Aerospec Technologies, the industry leader in report turnaround time, can generate a comprehensive report for farms up to 50MW within 72 hours and can provide reports for areas that need urgent attention within hours. The ability to act swiftly and decisively is an advantage for asset managers, especially during commissioning inspections when time is critical. One client told Aerospec that they faced a financial penalty of $97,000 per every day that commissioning was delayed. In these instances, the speed of inspection and report delivery is crucial.
The speed and completeness of aerial inspection slashes technician labor costs while providing a more comprehensive view of system performance. Combining money saved on technician’s wages with performance gains from proactive maintenance, O&M managers will likely find that aerial inspections lead to increased revenue. After calculating the cost of both manual and aerial inspection methods as well as forgone profits stemming from broken modules, Aerospec estimates that implementing regular aerial thermographic inspections into maintenance procedures can save O&M managers approximately $1,916 per MW per inspection compared to traditional field walks.
That’s a whole lotta dough.
If you are interested in learning more about how aerial thermography can reduce labor costs and increase your yield, visit www.aerospec.us today for more information or to schedule a demo.